I. Introduction:
In recent years, the state has vigorously promoted the development model of circular economy, advocated the establishment of a resource-saving society, and focused on the efficient use and recycling of resources, characterized by low consumption, low emissions, and high efficiency, in order to effectively use resources and the environment. The new economic development model based on protection is on the rise. Steel barrel manufacturing companies have also demanded energy conservation and emission reductions to reduce costs. For this reason, we have strengthened the research and development of steel drum drying and solidification equipment and achieved success. This year, two users across the country have used the new type of double bridge oven and curing oven designed and manufactured by the company. With coal as fuel, it is easy to use and has remarkable energy saving effect. It has been well received by all parties.
We are a scientific research unit under the Xi'an Science and Technology Bureau. We are mainly engaged in the research and development of steel drum production equipment. We are a national steel drum manufacturing equipment manufacturer and a member of the China Packaging Association. We have a complete steel drum production line (front and rear sections). The design and manufacturing capabilities of the second and last paragraphs have long been devoted to the research and development of steel drum equipment, technologies and processes, and many technologies have taken a leading position in the industry.
Second, the existing drying curing equipment problems:
Post-processing of steel drums requires phosphating, cleaning, drying, spraying, and curing. Therefore, ovens and curing ovens have become the key equipment for the processing of steel drums.
Traditional ovens, curing ovens occupy a large area, equipment costs are high, fuel uses electricity, oil, natural gas, etc., high energy consumption, high maintenance costs, and high production costs. There are many mechanical transmission links and more failure points.
In recent years, we have conducted research on industrial ovens in other industries, combined with the characteristics of the steel drum manufacturing industry, designed and developed double-bridge ovens and curing ovens. The use of several steel drum plants proves that it has the characteristics of transmission, energy saving, small footprint and low production cost.
Third, double bridge oven, curing furnace structure and production process:
The structure is shown in Figure 1 (see Figure 1):
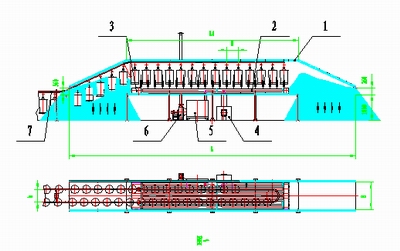
1. Bridge body 2. Transducer 3. Dust removal port 4. Coal-fired furnace 5. Collector dust collector 6. Induced fan 7. Suspension conveyor chain
production process:
After the coal-fired boiler is ignited, the dry air in the heat pipe of the transducer is heated, and under the action of the induced draft fan, the heated air flow circulates in the pipe, heat is dissipated through the surface of the heat pipe, and the temperature in the bridge box rapidly rises. The bridge box is equipped with a temperature control device. When the desired temperature is reached, the induced draft fan is automatically turned off. Since the transducer is built-in, the heat it emits is in the furnace, maximizing the use of energy.
Fourth, the mechanism:
During the drying process, due to the small proportion of the hot gas flow, it floats, and the moisture ratio is significant, sinks downward, and is automatically discharged from the exits of both ends of the double bridge.
The temperature rises quickly, and it takes only about 30 minutes from ignition to the desired temperature. Thermal insulation performance is good, because the proportion of hot air flow is small, float, stored in the bridge box, no spill, so the loss is small. After the production is completed, the fire source is sealed. When the engine is turned on the next day, the temperature in the furnace is reduced by only about 20 to 30°C.
The capacity of the bridge box is determined according to the size of the production capacity, and the design thermal power is calculated as 2500 kcal/M3 and the maximum temperature 300°C.
Due to the different types of paint used by each drum manufacturer, the furnace temperature settings are also different and can only be determined during the production process. If the pure drying, the northern region can be controlled at about 100 °C summer, and the curing according to the general standard requires 182 °C, 40 minutes of baking conditions, can also be cured at 225 °C conditions 10-15 minutes.
Under normal conditions (drum production capacity: 4-5 pieces/minute), the total designed heat power is approximately:
Drying furnace: 6-10 million kcal/hour
Curing oven: 30-40 kcal/hour
Air flow in the pipeline: 5000-7000M3/hour
Wind pressure: 700-900Pa
Transmission: Suspension conveyor chain, pitch t = 200mm, single point hoist 32kg, power 2.2KW (chain length 120m), frequency control. With a flexible layout (if required, in principle the workpiece can be transported to any station, but also can be turned multiple times).
As shown in Fig. 2 (see Fig. 2), it is a three-track bridge curing oven designed for another steel drum plant. It has the characteristics of low power, long transmission distance, etc. It is widely used in other industries such as automobile manufacturing industry and is a mature technology. The steel drum is hung on the hanging chain through the hanger, the opening is upward, and the steel drum runs downwards when the steel drum is exported. The hot air in the drum floats and returns to the inside of the bridge box, which greatly reduces the amount of the steel drum brought out during operation. Heat. The traditional method of opening down, the hot air filled in the steel drum can not overflow, in terms of 200L drums, each out of a bucket brings out 200L hot air, the heat loss can be imagined, the chain is used from Walking lubrication, simple and convenient.
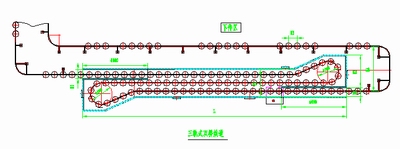
Flue gas temperature: Generally speaking, the exhaust temperature is greater than the temperature inside the bridge, up to 200-300 °C. Otherwise, the flue gas will bring out the heat in the bridge box. For this purpose, we set up a heat collecting box at the exit, and use the residual heat of the flue gas to heat the circulating water in the box, and this part of the hot water can be used for the degreasing bath or Used to bathe workers. In this way, the flue gas can be controlled below 150°C, making full use of energy.
Smoke and dust removal: Dust collection box is set in the bridge box, water film dust removal mechanism is set at the exit, no black smoke is emitted, and the indicators such as Ringermann blackness have met the requirements of the environmental protection department.
Furnace body: The furnace body is built with refractory bricks, plus an insulation layer. Double hearths are used and secondary air intake is added so that the coal can be fully burned.
V. Economic benefits:
Standard coal is calculated at 5,000 kcal/Kg. A 300,000 kcal double bridge curing oven consumes about 50 Kg/hour of coal per hour, and Xi'an has bituminous coal prices of about 400 yuan/ton, which amounts to about RMB 20/hour. The fuel costs of many steel drum plants in the region are all above 200 yuan/hour, the difference between the two costs is 10 times, and the economic benefits of coal-fired double-bridge solidification furnaces are significant.
Sixth, our proposal:
In view of the environmental protection and energy saving requirements, it is recommended to invest a certain amount of funds and manpower in the enterprises of this industry to carry out the necessary transformation of the oven and curing oven in the steel drum post-treatment equipment in order to achieve energy conservation and cost reduction. Newly built companies pay attention to this technology during the initial selection of the production line, so as to avoid the old way of wasting energy and increasing costs.
Welcome steel barrel business experts and leaders to visit us and discuss the new process and new technology issues of the steel barrel post-processing equipment.
Information: The Xi'an region is relatively cold in the winter. In the past, coal-fired boilers were used for heating, and the air pollution was serious. In the 1990s, it was forcibly dismantled and used oil-fired boilers. As oil prices continue to rise, users find it difficult to afford, and then use natural gas boilers. However, heating costs remain high, coupled with limited natural gas reserves, limited supply, can not meet the winter heating, in recent years replaced with new environmentally friendly coal-fired boilers, energy saving and environmental protection The benefits are significant and are growing rapidly.