Machining and tool selection for high chromium cast iron
High-chromium cast iron is a high-hardness and high-strength high-alloy white cast iron with anti-wear and anti-corrosion properties. High-chromium cast iron is used as a wear-resistant casting without any heat treatment. The hardness is generally above HRC45, and the tensile strength is 650 - 850MPa.
High-chromium cast iron is one of the difficult-to-cut materials. Carbide tools are difficult to process normally. Ceramic tools are generally used only for finishing because of the high brittleness. Before the 1990s, they were limited to some extent due to the difficulty of cutting. With the application of high-chromium cast iron, with the advent of new tool materials, the machining tools of high-chromium cast iron industry have experienced the process from cemented carbide to composite ceramics to cubic boron nitride materials, which has changed the high chromium to some extent. The investment in machining processes and equipment for cast iron machines has also brought about the prosperity of high-chromium cast iron castings as anti-wear castings in the industrial manufacturing field.
Before 2003, due to the limitation of tool materials, cemented carbide tools and composite ceramic tools were the mainstream of processing high-chromium cast iron. The processing route of high-chromium cast iron was generally: blank-softening treatment (reduced hardness)---roughing-- -- Heat treatment (increased hardness) --- finishing. It can be seen from the process route that two heat treatments and two clampings not only increase the workload, but also affect the processing efficiency and increase the machining cost. According to statistics, only softening treatment and two machining operations increase the cost by 2,500 to 3,000 yuan / ton. The BN-K1 grade cubic boron nitride tool developed by Valin Superhard in 2003 is higher in hardness than cemented carbide and ceramics, and its fracture resistance and fracture resistance are higher than ceramic tools. It is used as a tool for high hardness cast iron. It is widely used in the roughing, interrupted processing and finishing of high hardness cast iron of 35HRC-68HRC.
Compared with ceramic inserts, BN-K1 grade boron nitride inserts generally have a hardness of about 3500 HV, which is twice that of ceramic inserts and four times that of alloy inserts. The heat resistance of BN-K1 grade can reach 1400-l500 °C. When BN-K1 grade is processed high-chromium cast iron, the hardness at 1000 °C is higher than the normal temperature hardness of ceramic and hard alloy, high-speed cutting high hardness white When the cast iron is Cr26, the wear resistance of the BN-K1 grade tool is 25 times that of the silicon nitride ceramic, the impact resistance is more than 2000 times that of the silicon nitride ceramic, and the tool life can reach 22-30 times of the silicon nitride ceramic. . Therefore, the cutting parameters of the BN-K1 tool cut the superalloy and the hardened steel at a speed 3-5 times higher than that of the cemented carbide tool, which also creates conditions for the high-speed cutting of the PCBN tool. Due to the performance characteristics of the BN-K1 grade cutter, the high-chromium cast iron blank does not need to be softened and then rough-processed, and there is no need to perform secondary clamping, which changes the machining process and is widely used in high-alloy cast iron rolls and pump parts. , high-chromium cast iron lining and other wear-resistant castings.
Cutting parameters and cases of Hualing tool processing high chromium cast iron
In the machining process, in addition to the rational selection of cutting tools, the selection of cutting parameters for the tool is also one of the important factors for high-efficiency machining of high-chromium cast iron.
Among the three cutting factors of knife depth, cutting amount and cutting line speed, increasing the cutting depth is undoubtedly one of the effective means to improve the processing efficiency, and for some large pump parts, metallurgical and mining machinery wear-resistant castings, cutting amount Large, to improve processing efficiency, you must increase the depth of cut. Due to the fracture strength and resistance to breakage of the BN-K1 grade tool, the BN-K1 grade is more suitable for using a larger depth of cut to reduce the number of passes to improve machining efficiency compared to ceramic tools. At the same time, because of the high hardness and high temperature wear resistance of the BN-K1 grade, high-speed cutting can be performed with a cutting speed of 3-5 times that of cemented carbide and ceramic tools. The following are typical processing examples of Valin cutters in the high hardness cast iron industry:
1. Take the outer circle of the BN-K1 grade intermittent turning slurry pump impeller. Since the high-chromium cast iron impeller has 5 blades, there are intermittent cutting when machining the outer circle and the end surface. The cutting parameters of the BN-K1 grade tool are: vc=75m/min, ap=5mm, f=0.1mm/r. In the cutting process of this high-chromium cast iron part, the tool must withstand 5 impacts per revolution of the impeller, and one blade must withstand more than 3,000 impacts in one pass. The results show that there is no fracture and fracture during the intermittent processing of BN-K1 brand boron nitride tools. One blade is equivalent to 25 ceramic blades, which fully demonstrates the impact resistance of boron nitride tools, which not only reduces the cost of tool use. Processing efficiency has also increased by a factor of five.
2, taking BN-K1 grade tool milling high chromium cast iron liner as an example, cutting parameters: rough milling processing vc = 55m / min, ap = 2.5mm, feed per tooth fr = 0.25mm / r. The dimensions of both ends were the same, and there was no retraction and tool wear. Milling with ceramic tools requires 5-7 knives to complete, and the blade edge wears faster during cutting, resulting in increased cutting resistance and retraction, which seriously affects the quality and processing efficiency of the machined surface.
3, taking BN-K1 grade processing high nickel-chromium chilled cast iron roll as an example, the amount of cutting can reach 1mm / r, the depth of the knife is 10mm, the surface of the roll is abandoned, and it encounters sand, casting hard point does not collapse The knife, without breaking, shows that the BN-K1 grade has excellent toughness.
4. For the finishing of high-chromium cast iron, taking the high-chromium cast iron valve seat as an example, the BN-K11 grade in the Hualing HLCBN series can achieve high-speed finishing of Vc=180m / min.
With the development of boron nitride tool grades, as of 2014, Valin has five types of tool grades for the processing and development of high-hardness cast iron, which are suitable for processing in various working conditions, as shown in the figure:
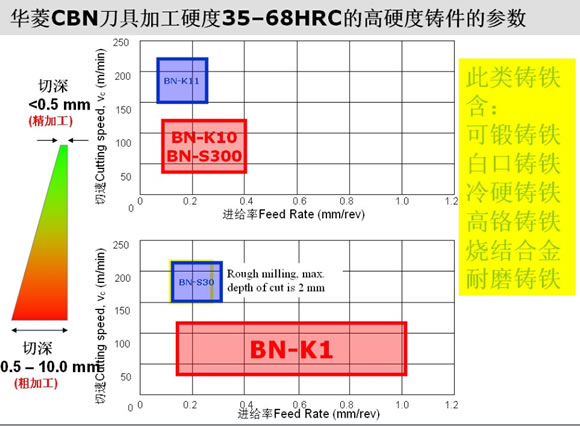
Hualing is super hard. As the pioneer of the localization of cubic boron nitride tools in China, it is one of the most well-known tool brands in the difficult material processing industry. Its tools are not only used for high hardness castings, but also for hardened steel, sintered alloys, etc. Cutting materials and high-speed cutting in the field of ordinary cast iron parts.
H1 Led Headlight,H1 Headlight Bulb,H1 Headlight,H1 Led Light
CHANGZHOU CLD AUTO ELECTRICAL CO.,LTD , https://www.cld-led.com