At present, domestic karts (similar to bumper cars) are imported from abroad, and aluminum alloy wheels are an important part. In the past, the castings were produced by pressure casting in foreign countries, and the castings were of poor quality, with low yield and high labor intensity. In view of the structural characteristics and performance requirements of the casting, how to improve its product quality, reduce raw material consumption, save energy, improve labor productivity and reduce casting cost is the key in current production. From the development situation, it is known that the use of extrusion casting instead of pressure casting is an effective process for manufacturing aluminum alloy wheels in the future.
1 Wheel material, requirements and casting design
Figure 1 shows a diagram of the aluminum alloy wheel parts. Not only do the wheels have high performance requirements, but the shape is very complex.
Figure 1 Wheel parts drawing
The chemical composition (mass fraction) of the wheel material is: 1.5% to 3.5% Cu, 10.5% to 12.0% Si, <0.3% Mg, <1.0% Zn, <0.5% Mn, <1.3% Fe , <0.5% Ni, <0.5% Sn, and the rest is Al. Mechanical properties: σb>276 MPa, σs>115 MPa, σ>4.4%, HB>92.
The dimensional accuracy of the inner shape of the wheel is high, and the machining allowance and the remaining block should be added. According to the requirements of the extrusion casting process, the shape of the wheel parts with complicated shapes is designed as shown in Fig. 2.
It can be seen from the figure that in order to facilitate the removal from the inner hole of the casting and to simplify the machining of the mold, the original stepped shaft hole is designed as a cylindrical central hole having a diameter of î€Ï†30 mm and an inner wall inclination of 3° [1].
Figure 2 Wheel casting diagram
2 mold structure and design parameters [1]
2.1 Squeeze casting mold structure
The die structure of aluminum alloy wheel extrusion casting is shown in Figure 3. It mainly has a cavity, a right die, a ram insert and a left die to form the required cavity. The left concave mold and the right concave mold are respectively fixed on the left concave mold template and the right concave mold template, the left concave mold template is fastened to the lower template by screws, and the right concave mold template is opened on the guide column through the side cylinder. And closed.
Figure 3 wheel extrusion casting mold
1. Upper template 2. Punch fixing plate 3. Punch 4. Guide post 5. Right concave mold 6. Right concave mold template
7. Backing plate 8. Lower template 9. Top rod insert 10. Left concave mold 11. Left concave mold template
The 2000 kN hydraulic press is used for extrusion casting. The working process is: after the quantitative alloy melt is poured into the groove, the punch fixed on the movable beam is pushed into the cavity at a certain speed, and the pressure reaches a certain value. The pressure is maintained; after the aluminum alloy is solidified, the pressure is released, the punch moves upward through the return stroke of the working cylinder, and the ejector insert is withdrawn from the inside of the casting through the lower top cylinder until all of the casting is removed, and then the right concave mold is opened by the side cylinder, and taken out. casting.
Next page
Product Name: silicon carbide coated multi grid abrasive sandpaper wet or dry sandpaper
Material: Silicon carbide
Size: 230mm x 280mm, 93*230mm
Substrate: Paper backing
Grit: 60#, 80#, 100#, 120#, 150#, 180#, 240#, 280#, 320#, 360#, 400#, 500#, 600#, 800#, 1000#, 1200#, 1500#, 2000#, 3000#, 5000#, 7000#
Coating: Electro coated
Feature: Waterproof, flexible, dual use, durable, cost-effective.
Application: Used for grinding and polishing metal, wood, glass, ceramics, plastic, varnish, stone, wall etc.
Grinding & Polishing Sandpaper
Soft Paper Backing / Uniform Sand / Wet & Dry Use
How to Choose Grit
From 60# to 2000#
Grit Size Introduction Suitable for
60# - 220# coarse sand, for hard and rough products Metal, wood, wall, stone
240# - 500# Frequently used, for secondary grinding Wall, furniture, stamp
600# - 1500# Fine sand, common used for grinding and polishing Metal, bodhi, amber, honeystone, jade and plastic
2000# and above Super fine, for polishing Amber, honeystone, bodhi, metal, nail, mirror polish etc.
Packing Details: 100 pcs/box, 1000 pcs/CTN.
Lead Time: For small quantity, 3-5 days after payment done.
For large quantity, can be negotiable.
Delivery Methods: by sea, air, expresses like DHL, Fedex, UPS, EMS etc.
The related abrasive products we can supply is Flap Disc Adhesive, Abrasive Flap Disc , and Flap Disc Making Machine, Flap Wheels , Flap Wheel Machine , Abrasive Sanding Disc, if you have any needs about abrasive tools, please kindly feel free to contact us.
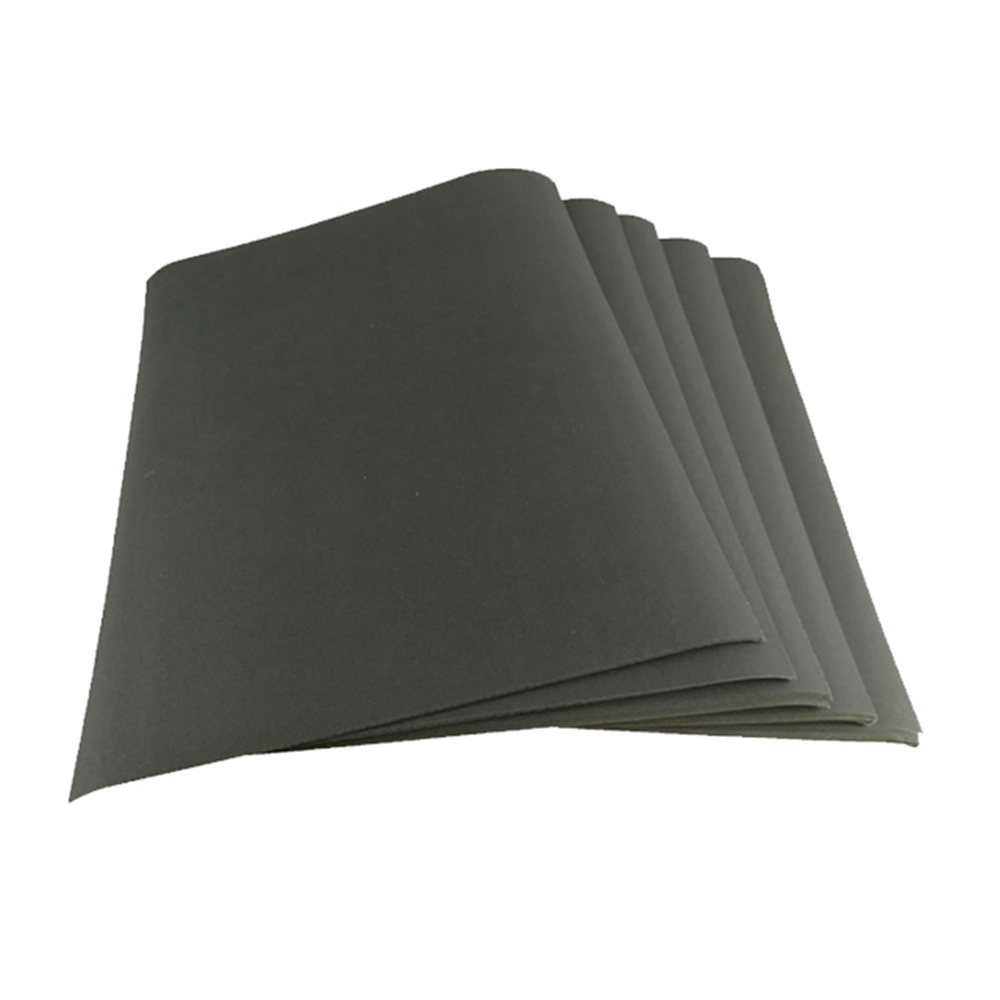
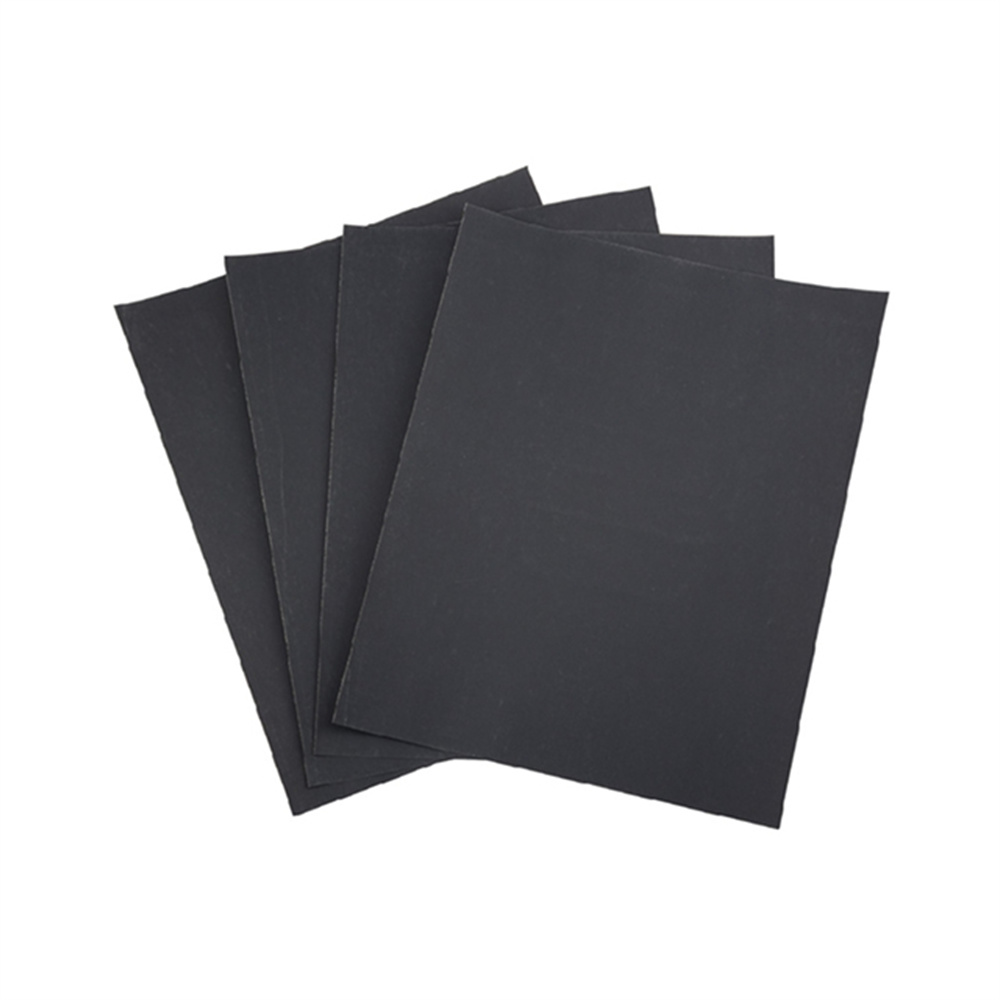
Abrasive Sandpaper,waterproof sandpaper,Electric Sandpaper,Sandpaper Waterproof,Silicon Carbide Sandpaper
Zhengzhou Jiading Abrasive Manufacturing Co.,Ltd , https://www.jd-abrasives.com