High-temperature melt pressure sensors are very sensitive components that can only be fully utilized if they are properly installed and maintained.
In the extrusion process, some quality standards of the product (such as dimensional accuracy or surface flatness of mineral filler parts) require optimal control of the extrusion pressure, which is achieved by a high temperature melt pressure sensor. Important components required. By providing a melt pressure sensor and a pressure control device at the mold inlet connection, the yield can be made more stable while reducing material waste. Melt pressure sensors play an important role in improving melt quality, increasing production safety, and protecting production equipment and extending their service life. In addition, measuring the pressure through the filter and the melt pump is also important to ensure production safety and to optimize the performance of the equipment. If the melt is blocked when it flows into the mold, the sensor under the filter will alert you to the operator. When the sensor on the filter screen gives an alarm, it indicates that the internal pressure of the extruder is too high, which may cause excessive wear on the screw. For the manufacturer of the melt pump, it is necessary to measure the inlet pressure and outlet pressure of the melt to ensure that the melt can continuously flow into the mold, as any hindrance can cause damage to the melt pump.
The high temperature melt pressure sensor assembled on the extrusion line can be a single sensor that measures only one point pressure, or a series of sensors that measure the entire production line. The melt pressure sensor is connected to the data logger and the audible alarm device, and the processing parameters of the extruder can be adjusted by the processing control system. At the same time, the pressure sensor is also a very sensitive component that can be easily damaged if it is not properly installed and maintained. The following simple methods are helpful to extend the life of the pressure sensor and help the user to obtain accurate and reliable measurement results.
â— Correct installation
Usually the damage of the high temperature melt pressure sensor is caused by improper installation position. If the sensor is forcibly installed in an excessively small hole or an irregularly shaped hole, the vibration film of the sensor may be damaged by impact. Choosing the right tool to machine the mounting holes will help control the size of the mounting holes. In addition, suitable mounting torque facilitates the formation of a good seal. However, if the installation torque is too high, it is easy to cause the high temperature melt pressure sensor to slip. To prevent this, it is common to apply the anti-separation compound to the threaded portion before the sensor is installed. After using this compound, the sensor is difficult to move even if the mounting torque is high.
â—Check the size of the mounting hole
If the size of the mounting hole is not suitable, the threaded portion of the high temperature melt pressure sensor is susceptible to wear during installation. This not only affects the sealing performance of the device, but also prevents the sensor from functioning fully and may even pose a safety hazard. Only the proper mounting holes can avoid thread wear (Thread Industry Standard 1/2-20UNF2B). Mounting holes can usually be tested with a mounting hole gauge to make the appropriate adjustments.
Concerned about surprises
Label: High temperature melt pressure sensor installation and maintenance knowledge
Previous: Pressure sensor, transmitter knowledge and answer Next: Various hardware installation
Due to its wide range of uses, there are also many varieties of hook and loop sanding disc. The most commonly used are red sanding disc, yellow/gold sanding disc, green sanding disc, and white sanding disc, etc.
The sandpaper disc is using aluminum oxid abrasives, with grits as below: 40#, 60#, 80#, 120#, 180#, 240#, 320#, 400#, 600#, 800#, 1000#, 1200#, 1500#, 2000#.
The abrasive polishing disc can be punched into various shapes, round, round with holes, triangle, rectangle, iron shape, neckline shape, etc.
This product is round abrasive disc size: 100mm, 125mm, 150mm, 180mm, 225mm or other size can be customized.
The holes best selling is with 6 hole, 8 holes, 15 holes, 17 holes or customized.
The main purpose of our abrasive sanding disc:
1. Polishing of primer and finishing of paint, such as mid-coat paint/primer grinding of ships.
2. Polishing of synthetic materials, such as burr sharp edges and surface adjustment after plastic products are formed.
3. Grinding of metal and aluminum alloy to remove foreign matter and surface particles.
4. Suitable for making various specifications of brushed and self-adhesive sand discs.
This abrasive sanding disc is one of our main abrasive products, as the manufacture of abrasive tools, we mainly produce the Flap Disc Backing Pad, Flap Disc Adhesive, Abrasive Flap Disc, Bonded Abrasives ( Cutting Wheels and Grinding Wheels ), Abrasive Machine , etc. So welcome more orders, we can offer you best quality product with best competitive price, please contact Emma.
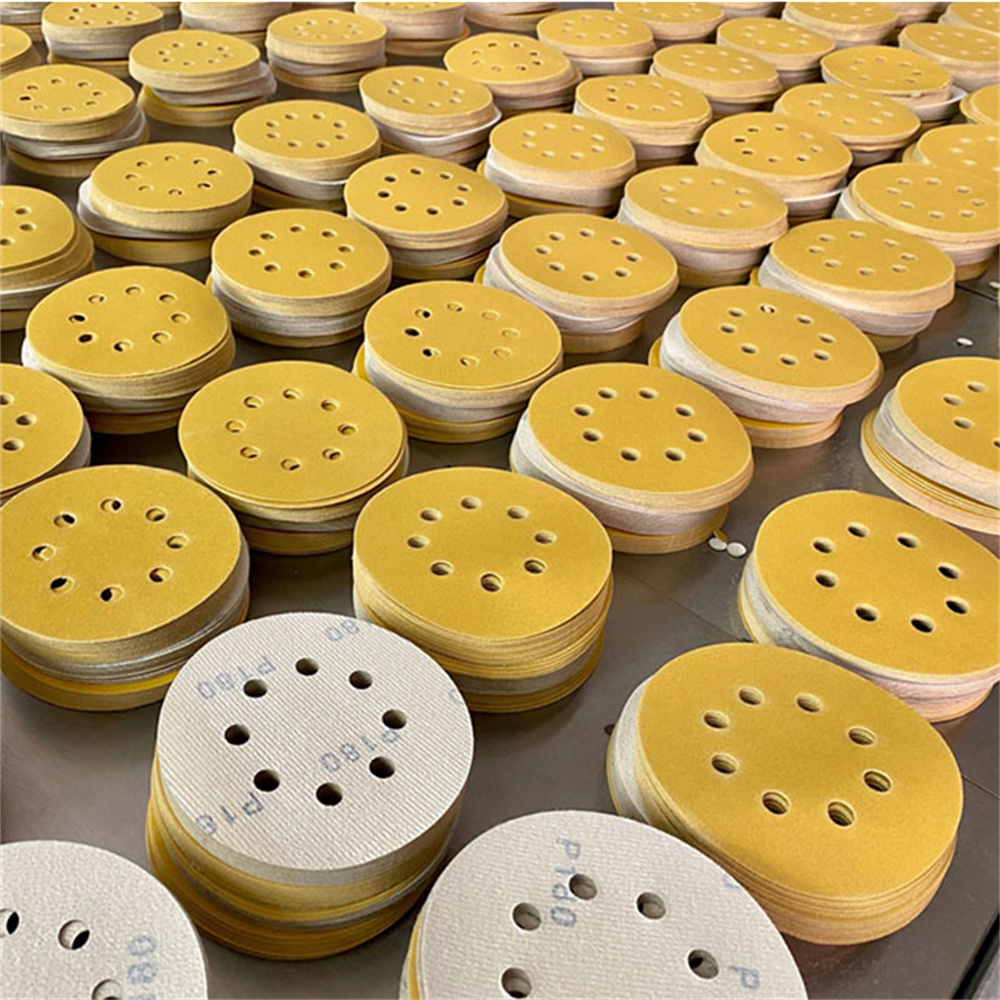
Abrasive Sanding Disc,Sanding Disc,Metal Sanding Disc,Abrasive Tools Sanding Disc
Zhengzhou Jiading Abrasive Manufacturing Co.,Ltd , https://www.jiadingabrasive.com