In recent years, with the wide application of robotic automatic welding technology in the construction machinery industry, higher requirements have been placed on the cutting precision and quality of the blanking parts. The traditional cutting equipment can no longer meet the requirements of automatic welding and high precision assembly. At the same time, with the rapid advancement of the national “industrialization and informationization†guidelines, the application of intelligent and information-based cutting equipment in modern construction machinery manufacturing plants has become the mainstream of enterprise development.
Application Status of Cutting Technology in Construction Machinery
1. Characteristics of the cutting parts and process requirements
Cutting and welding are inextricably linked in the construction machinery manufacturing industry. The quality of the cutting directly affects the welding quality. At the same time, with the wide application of robotic automatic welding technology, some new requirements are put forward on the cutting quality of the plate.
In summary, the construction machinery industry has the following features:
First, the construction machinery cutting parts are mostly low carbon steel (Q235), low alloy high strength structural steel (Q345), and less use of non-ferrous metals and non-metals.
Secondly, the welded structural parts are mostly made of medium and thick plates, and the cutting work is large. For example, the plate with a thickness of 8~30mm accounts for more than 80% of the total consumption of engineering machinery steel.
Third, the cutting member has a complicated shape and a large size, and is easily deformed after cutting.
Fourth, with the wide application of robotic automated welding technology, the control requirements for cumulative size and dimensional accuracy of sheet-related dimensions are more stringent.
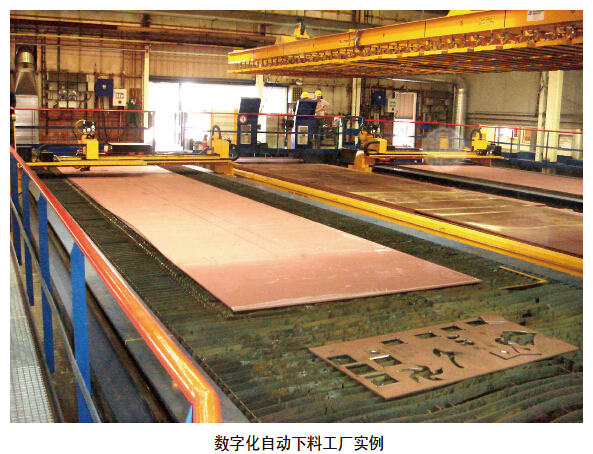
2. Cutting technology application
In view of the technical requirements of the cutting parts in the construction machinery industry, combined with the characteristics of the cutting equipment, the three major cutting technologies of flame, plasma and laser are widely used in engineering machinery manufacturing enterprises. With the rapid development of cutting technology and the continuous improvement of the overall performance of cutting equipment, the status quo of plasma and laser cutting technology and flame cutting are gradually formed.
The following features are formed in equipment selection and application:
(1) Collaborative application of three cutting equipments, the division of labor is more clear In the engineering machinery industry, flame cutting equipment has been widely used in the past, but with the rapid development of cutting technology, plasma and laser cutting technology have occupied a dominant position. At present, the industry basically divides according to the thickness and dimensional accuracy requirements of parts: fine plasma cutting equipment is mainly used for cutting 8~25mm thickness, and it is economical and efficient to use fine plasma cutting in this thickness range; laser cutting equipment Mainly used for the cutting of thin plates below 8mm. However, for some medium and heavy plates with high dimensional accuracy and high quality requirements, laser cutting can also be used. For example, the boom and the arm of the excavator manufacturing enterprise generally use laser cutting, which is mainly due to the high dimensional accuracy of the laser cutting. And the cutting heat affected zone is small. However, medium-thickness laser cutting is less efficient than plasma cutting; flame cutting is mostly applied to the cutting of 25mm or more plates, which can fully exert the advantages of high efficiency and low cost of flame cutting.
(2) The general use of fine cutting technology With the promotion and application of modern automatic welding equipment, such as Carter, Xugong, Sany and other enterprises have introduced a highly automated robotic welding flexible production line, which requires more and more dimensional accuracy of the blanking process. high. At present, fine plasma and laser cutting technology is widely used in the industry to improve the dimensional accuracy of the blanking parts. In addition, for some small hole processing, the industry generally adopts laser cutting forming, which eliminates the subsequent drilling process. At present, in the engineering machinery cutting equipment, the occupancy rate of fine plasma and laser cutting equipment has reached more than 80%.
(3) Efficient cutting has gradually become a major feature of the engineering machinery industry. At present, the engineering machinery industry widely adopts efficient multi-head cutting equipment, which makes the cutting efficiency double. Most engineering machinery manufacturers use double-head or four-head plasma cutting equipment, and even some enterprises use 12-head flame cutting equipment to improve the cutting efficiency of thick plate cutting parts.
(4) High-power, large-format has become another major feature of equipment selection. Due to the large size of engineering machinery components, the selection of wide-format cutting equipment has become the mainstream of equipment selection. At present, most of the industry uses 6.5m × 24m multiple devices to improve the effective utilization of equipment. In addition, in terms of cutting power supply, plasma cutting equipment mostly uses Hypertherm 260, 400 and Kelbay 280, 360 high-power plasma power supply; laser cutting equipment mostly uses 4kW high-power CO2 laser generator.
More exciting content Welcome to Metalworking Online》》》Essen Special Report
The 19th Beijing Essen Welding & Cutting Fair
Development trend of blanking factory in construction machinery industry
With the upgrading of the manufacturing level of the construction machinery industry, some drawbacks of cutting technology are also increasingly exposed. At present, the construction machinery blanking factory mainly has the following problems: 1 workers have high labor intensity and poor working environment, especially the smoke in the plasma cutting process has a great influence on the physical and mental health of the operator. 2 The degree of automation in the cutting process is low, requiring manual loading, blanking and dip. 3 Single equipment working independently of each other is not conducive to the digital management of the factory. In response to the above problems, a new technology - digital automatic cutting factory came into being.
1. System composition of digital automatic cutting factory
The digital automatic cutting factory consists of CNC cutting equipment, intelligent driving, steel plate transfer trolley, production management system and warehouse management system, which realizes automatic control of upper board, cutting and blanking, and realizes continuous cutting and remote information of cutting machine (including Real-time dynamic monitoring of main cutting parameters, allocation of cutting tasks, task completion, etc. Digital automatic cutting is a high-tech developed on the basis of cutting equipment. It is a digital cutting factory that integrates automation, informationization and high efficiency, and leads the development direction of the blanking factory. At present, the shipbuilding industry in foreign countries has begun to be widely promoted and applied, and is still in its infancy in the domestic construction machinery industry.
The specific tasks of each component of this system are as follows:
(1) Intelligent driving 1 lifts the steel plate on the transport vehicle to the pre-processing storage area. 2 Lift the steel plate to be pre-processed to the pretreatment equipment. 3 Lift the finished steel plate to the area to be cut. 4 Lift the steel plate in the area to be cut to the cutting table. 5 Lift the plate on the cutting table to the decomposition table.
(2) Laser automatic positioning and automatic cutting of the cutting equipment. After the cutting is completed, the cutting information is fed back to the intelligent driving, and the intelligent driving is automatically cut.
(3) The Production Management System (MPM) is responsible for the management of production orders, parts libraries, sheet libraries, parts libraries, and cutting schedules.
(4) The Warehouse Management System (WMS) directs the intelligent driving to lift the steel plate from the conveyor and transport it to different storage locations. The WMS will optimize the transportation route according to the transportation needs.
2. Digital automatic cutting factory features
The application of the digital automatic cutting factory will break the traditional production organization mode, the operators will be freed from the heavy manual labor, and the production decision, plan management, order production, material storage are all digitally managed, and the production personnel only need to Optimized supervision in the factory management system has truly realized the deep integration of “industrialization and informationization†advocated by the state. In addition, the continuous utilization of cutting equipment, the automatic matching rate of logistics equipment and cutting equipment, and the optimal execution of production plans have greatly improved production efficiency. In view of the above characteristics, the digital automatic cutting factory will become the development direction of the future cutting factory, and bring a qualitative leap to the development of the construction machinery industry!
More exciting content Welcome to Metalworking Online》》》Essen Special Report
The 19th Beijing Essen Welding & Cutting Fair
Fuonce-Lighting , https://www.fuoncelighting.com